Development of a New Principle Printing Technique That Allows Easy, High-speed, and Large-area Manufacturing of Ultrafine Electronic Circuits
- The new technology will accelerate conversion of our entire life scene environed by IoT and touch sensors -
TOKYO, Apr 19, 2016 - (JCN Newswire) - Toshikazu Yamada (Senior Researcher), Tatsuo Hasegawa (Principal Research Manager and Professor at the University of Tokyo), and others of the Flexible Electronics Research Center (Director: Toshihide Kamata), the National Institute of Advanced Industrial Science and Technology (AIST; President: Ryoji Chubachi), in collaboration with the University of Tokyo (President: Makoto Gonokami), Yamagata University (President: Kiyohito Koyama), and Tanaka Kikinzoku Kogyo K.K. (President; Akira Tanae), have developed an epoch-making new printing technology called "SuPR-NaP (Surface Photo-Reactive Nanometal Printing) technique", which enables production of ultrafine silver wiring patterns only by patterning using ultraviolet irradiation and subsequent surface coating of silver nanometal ink that includes silver nanoparticles at high concentration.
 | Figure 1: Schematic of the SuPR-NaP technique
(1) masked ultraviolet irradiation, (2) latent image formation of activated surface, (3) blade coating of silver nanometal ink, (4) self-formation of the silver wiring pattern. |
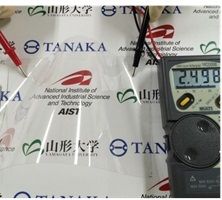 | |
Print production - or printed electronics - technology for highly fine metal wiring that is indispensable for fine electronic circuits has faced several technological difficulties such as in reproducibility due to the contamination of printing plates or other apparatus, in sintering or fusion of metal particles on substrates after printing, in avoiding distortion of plastic substrates by high-temperature post-treatment, and in avoiding peeling off the printed wires due to the substrate bending. The developed technique utilizes selective chemisorption phenomenon of silver nanoparticles, included in the silver nanometal ink, on an activated surface produced by ultraviolet irradiation, which is followed by the self-fusion reaction between nanoparticles to afford low-resistance silver wiring. This technique enables easy and rapid production of ultrafine electronic circuits over a large-area substrate without using vacuum, with minimum linewidth of 0.8 um that strongly adhere to the plastic substrates. A flexible touch-screen sensor produced by this technology is now planned to be in practical use, and is demonstrated this time by an 8 inch trial product. The details of this study will be published on April 19, 2016 in a British online scientific journal, Nature communications.
Social Background of Research
The "printed electronics technology" which takes advantage of printing methods for manufacturing various electronic devices may enable device productions without vacuum and at around room temperature, so that it is expected as a key technology to accelerate prevailing flexible and large-area human interface devices and thus to realize computerization of our entire life scene. Developments of inks and printing techniques are now widely studied, in order to realize print production, in particular, of fine metal wiring that is indispensable to compose fine electronic circuits. As the ink for metal wiring, most promising is silver nanometal ink that includes silver nanoparticles of 10-100 nm (nm is a length of one billionth metre) diameter at high concentration. In order to preserve the ink stability, the nanoparticle surfaces are covered by encapsulating layers. In recent years, manufacturing methods of such silver nanometal inks have been advanced considerably, and the mass production of the inks is now possible. Printing production methods of metal wiring using silver nanometal inks, including screen printing, micro-contact printing, and inkjet printing, are also studied. However, the silver wiring manufactured by the printing so far does not reach the level required for its practical use, in terms of pattern resolution, conductivity, adhesivity to substrate, processing temperature, and manufacturing throughput, due to several reasons; the encapsulating layer of the silver nanoparticles causes difficulty in obtaining high quality and low resistivity silver wiring after the printing; the removal process of the encapsulating layer may damage the heat-sensitive flexible substrates; or a limitation in the adhering strength of ink droplets on a substrate surface or in the control of droplet volume. It is quite difficult to resolve these problems by improving the existent printing technologies. So it has been strongly required to develop an innovative printing technology that is based on a new printing principle to fully utilize the potential of the silver nanometal ink.
History of Research
AIST has been promoting the research and development of the printed electronics technology in a wide range of aspects. A part of the research and development has focused on the use of surface modification technologies of substrates on which ink is applied, in order to improve and sophisticate the printing techniques for producing semiconductor layers and ferroelectric layers (AIST press releases on July 14, 2011, October 31, 2012, and July 21, 2013, research results announced on July 14, 2015, and AIST press release on October 1, 2015). During the further studies to improve printing technologies of metal wiring by the surface modification technologies, the researchers found that when they use a specific silver nanometal ink (diameter of silver nanoparticles is about 13 nm) that is invented and developed by Prof. Masato Kurihara at the academic research institute (taking charge of the faculty of science) in Yamagata University (Press release on November 12, 2013, by Yamagata University) and is now being developed as industrial products by Tanaka Kikinzoku Kogyo K.K., the silver nanoparticles are selectively adsorbed through chemisorption on a certain surface-modificated substrate surface, and that the particles exhibit a particle-particle fusion reaction. Based on the analyses of this phenomenon, and also on the study of developing the printing technique based on the analysis, the researchers have finally reached the present achievement.
This study is supported partly by the Japan Science and Technology Agency (JST) through Strategic Promotion of Innovative Research and Development Program (S-Innovation), as "Development of Flexible Display based on AM-TFTs Manufactured by Printing Processes with New High-Performance Polymer Semiconductors" (Project Manger: Kazuo Takimiya, Group Director at Center for Emergent Matter Science of RIKEN), and also partly by the same agency through NexTEP Program, as "Touch Screen Sensor Film using Metal Wiring" (Implementing Company, Tanaka Kikinzoku Kogyo K.K.; Representative Researcher: Tatsuo Hasegawa). Acquisition of Yamagata University's intellectual properties related to the silver nanoparticles is supported by JST.
Details of Research
Figure 1 presents a schematic of the print production process for metal wiring by the developed SuPR-NaP technique. Firstly, ultraviolet light at wavelength of 172 nm is irradiated through a patterned photomask on an amorphous fluoropolymer layer fabricated on a substrate surface (Fig. 1 (1)). A latent image of a highly activated (or reactive) surface pattern that adsorbs silver nanoparticles via chemisorption is formed on the surface (Fig. 1 (2)). The whole substrate surface is then exposed to the silver nanometal ink by the blade coating technique, which results in the selective adsorption of silver nanoparticles on the activated surface (Fig. 1 (3)). Finally a fine silver pattern is obtained by self-fusion between the silver nanoparticles (Fig. 1 (4)).
Figure 2 presents microscope images of the obtained silver wiring. Silver wiring with minimum linewidth as small as 0.8 um is obtained. The resolution is several tens times higher than the products produced by screen printing or conventional inkjet printing. The thickness can be controlled within the range of 30 to 100 nm by controlling the ink concentration. In conventional printing techniques, the printed ink usually exhibits the coffee-ring effect where the peripheral area becomes extremely thick, which causes problematic difference between the actual and the designed resistance values of the printed metal wiring. In the developed technique, however, the obtained silver wiring exhibited constant thickness, irrespective of the linewidth, where the coffee-ring effect was not observed. It is found by the observation with a scanning electron microscope (SEM) that the thin silver layer is formed on the activated surface, where the spherical shape of silver nanoparticles disappears due to the fusion reaction between the nanoparticles. The obtained silver wiring is strongly adhered to the substrate surface with 5 MPa strength (50 times as high as ambient pressure). The obtained silver wiring exhibits enough high conductivity, reaching as high as one hundred thousand siemens per centimeter (one sixth of that of bulk silver), by the heat treatment at the temperature of 80 degrees Celsius that does not affect the flexible substrate.
The silver nanometal ink used in this study includes alkylamine encapsulated silver nanoparticles at high concentration with weight ratio in the range between 40 % and 60 %. It was reported by Yamagata University that when the silver nanometal ink is dried, encapsulating alkylamine molecules whose coordination strength is relatively weak are gradually left, and the aggregation and fusion of silver nanoparticles proceeds even at room temperature. By the use of the silver nanometal ink that exhibits such a peculiar characteristic, the innovative "SuPR-NaP" technique has been developed.
Carboxyl groups are generated due to the cut of chemical bonds of the polymer by ultraviolet irradiation on the fluoropolymer layer that is used as a surface layer of substrates. When the silver nanoparticles are contacted with the surface, they are directly connected with the carboxyl groups that form stronger bonds than with the encapsulating alkylamine molecules (Fig. 4). Many silver nanoparticles are trapped on the surfaces, and then the silver nanoparticles contacted with each other start to fuse. It was found, by the surface-enhanced Raman scattering measurement, that a layer of carboxyl groups is formed at the interface between the silver layer and the activated surface. It is considered that the fusion reaction between the silver nanoparticles would raise the temperature at the silver surfaces, so that the desorption of alkylamine molecules and the fusion reaction between the silver nanoparticles proceed by the avalanche-like process to eventually form a self-fused solid silver layer without voids (Fig. 3 right).
At present, transparent conducting electrodes with use of indium tin oxide (ITO) film are used for touch-screen sensors of smart phones, etc. However, such a sensor uses the hard crystalline oxide film which is easily broken when it is bent. It is also necessary to use vacuum in the production of the electrodes. Therefore, the oxide films have difficulty in terms of flexibility and low-cost production with saving materials. Because of the above reasons, it is now considered to develop transparent conductive electrodes by using network-like metal wiring that is composed of fine metal lines with likely-invisible linewidth of a few micrometres. With use of the developed printing technique, the researchers produced a flexible touch-screen sensor by fabricating silver wiring with a linewidth (2 um) which is close to the diffraction limit of visible light on a plastic substrate. The obtained touch-screen sensor presents a higher tolerance to bending, and is also better than other transparent conducting electrodes such as ITO, silver nanowires, or graphene, in terms of the transmittance and the sheet resistance (Fig. 5 right). The developed technology enables easy and rapid production of flexible touch screen sensor sheets without vacuum and at ambient pressure and room temperature and by environment-conscious manufacturing process that can minimize the consumption of the silver nanometal ink.
It is expected that this technology should be further developed as the technology which enables us to produce touch sensors only by sticking thin plastic films, as the crucial technology in the printed electronics to produce a variety of electronics devices by printing, and also as the new technology to produce patterned metal thin films easily by the applying technique.
Future Plans
Sample shipment of the flexible touch-screen sensor sheet by this technique is now planned to be begun in January 2017 by Tanaka Kikinzoku Kogyo K. K.
Press release (PDD): http://www.acnnewswire.com/clientreports/598/20160419.pdf
(Translation of AIST press release on April 19, 2016)
Sectors: Metals & Mining, Electronics, Science & Research
Copyright ©2025 JCN Newswire. All rights reserved. A division of Japan Corporate News Network.
|
Latest Release
 Mitsubishi Heavy Industries Achieves Highest-Ever Order Intake, Revenue, Net Income, and Free Cash Flow in FY2024, Increases Dividends, and Releases FY2025 Guidance May 09, 2025 18:57 JST
|  Valuufy Selected by Global Tech Leader for Environmental Impact Assessment May 09, 2025 18:00 JST
|  Mazda Adopts North American Charging Standard for BEVs launched in Japan May 09, 2025 16:03 JST
|  Mitsubishi Motors to Launch an All-New BEV Based on Nissan's Next-Generation LEAF in North America in the Second Half of 2026 May 08, 2025 11:25 JST
|  Mitsubishi Motors and Foxtron Sign MOU for OEM Supply of EV May 08, 2025 11:08 JST
|  Everest Medicines Announces NMPA Full Approval of NEFECON, Broadening Treatment Access for IgA Nephropathy Patients in China May 07, 2025 19:06 JST
|  Anime Tokyo Station: Mobile Suit Gundam GQuuuuuuX -Beginning- Special Exhibition May 03, 2025 03:00 JST
|  TOYOTA GAZOO Racing Set for Spa spectacle May 02, 2025 19:29 JST
|  FWD Group reports exceptionally strong first quarter new business update May 02, 2025 17:00 JST
|  Toyota Mobility Foundation, Bangkok Metropolitan Administration, UN-Habitat, Asian Institute of Technology and Toyota Motor Thailand Sign a Letter of Intent (LOI) to Launch the TRUST Project for Road Safety in Thailand May 01, 2025 17:48 JST
|  Katalon Officially Launches TrueTest(TM) - The First AI-Native Testing System That Thinks Like a Tester and Learns from Users Apr 30, 2025 17:20 JST
|  Eisai Representative Corporate Officer and CEO Haruo Naito Awarded the Order of the Rising Sun, Gold and Silver Star Apr 30, 2025 14:17 JST
|  Mitsubishi Shipbuilding Holds Christening and Launch Ceremony of Large Car Ferry KEYAKI in Shimonoseki Apr 29, 2025 17:24 JST
|  NEC DGDF Headquarters relocates to Zurich to accelerate growth and enhance management globally Apr 28, 2025 16:03 JST
| NEC achieves Japan's longest terrestrial wireless optical communication over 10 km Apr 25, 2025 17:50 JST
|  Olympus Appoints New CEO Apr 25, 2025 15:30 JST
|  DENSO Announces Year-End Financial Results Apr 25, 2025 12:17 JST
|  DENSO and DELPHY Sign Memorandum of Understanding to Develop Data-Driven Smart Horticulture Apr 24, 2025 18:43 JST
|  MyJCB App Wins "iF DESIGN AWARD 2025" Apr 24, 2025 17:00 JST
|  Fujitsu launches new company 1FINITY to strengthen network products business
Apr 24, 2025 16:24 JST
|
More Latest Release >>
|